신속한 설계 반복
엔지니어는 3D 프린팅 기술을 활용하여 다양한 디자인의 기능적 프로토타입을 신속하게 생성할 수 있습니다.
그런 다음 이 프로토타입을 다양한 구조적, 기능적 및 재료 특성에 대해 테스트할 수 있습니다. 결과에 따라 디자인을 수정할 수 있습니다.
3D 프린팅은 자동차 부품의 프로토타입을 만드는 시간을 크게 단축하여 신속하고 반복적인 설계 프로세스를 가능하게 했습니다.
예비 부품의 가용성
적절한 양의 예비 부품을 비축하는 것이 제조업체의 주요 비용 구성 요소가 되었습니다. 또한, 시장 출시 전략의 단축으로 인해 자동차 부품의 수명 주기가 단축됩니다.
3D 프린팅을 통해 자동차 부품 제조업체는 모든 예비 부품의 디지털 저장소를 유지하고 필요할 때 인쇄할 수 있습니다.
이제 제조업체는 더 오랜 기간 동안 제품 지원을 제공하여 제품 수명 주기를 늘릴 수 있습니다.
생산 리드 타임
자동차 부품에서 3D 프린팅 솔루션의 사용이 증가하여 틈새 수량에 필요한 복잡한 부품 및 부품의 생산 리드 타임을 가속화하고 있습니다.
툴링을 통한 시간 및 비용 절감은 제조업체의 또 다른 중요한 이점이며 일부는 섀시와 같은 부품을 직접 3D 프린팅하기 시작했습니다.
3D 프린팅 – 일본 자동차 산업 재정의
자동차 산업에서 가장 큰 회사 중 일부가 프로토타입 및 생산 노력 모두에서 적층 제조를 사용하고 있다는 것은 비밀이 아닙니다. 사실, 항공 우주와 함께 자동차는 이 기술의 첫 번째 채택자 중 하나였습니다.
자동차에 대한 요구가 높습니다. 고성능 부품에는 고성능 재료가 필요합니다. 과거에 이러한 회사는 프로토타입에서 설계 검증 및 최종 사용 구성 요소에 이르기까지 전통적인 제조 방법으로 제한되었습니다. 이러한 방법은 시간과 디자인의 자유도 모두에서 상당히 제한적인 것으로 알려져 있습니다.
적층 제조(3D 인쇄)의 등장으로 OEM, 부품 제조업체 및 애프터 서비스 제공업체를 위한 보다 유연하고 혁신적인 솔루션이 만들어졌습니다. 이 솔루션은 더 이상 프로토타입 제작에 국한되지 않고 최종 사용 부품 생산에 국한됩니다.
특수 차량용 맞춤형 부품
(주)산키도 예외는 아닙니다. 일본 이시카와 현에 위치한 SANKI는 특수 차량 캡과 구획 관련 부품을 생산합니다. 맞춤 설계 및 제조된 에어컨 통풍구와 같은 부품은 기존 시장에서 사용할 수 없습니다.
SANKI는 처음에 이 프로젝트에 사출 성형을 사용하는 것을 고려했지만 제한된 차량 수량을 감안할 때 이 대량 생산 방법은 적합하지 않았고 단위당 비용이 너무 높았습니다. 그들은 INTAMSYS FUNMAT PRO 410을 통해 3D 프린팅에 빠르게 시선을 고정하고 사출 성형 비용을 비교했습니다. 그들이 발견한 것은 사출 성형이 수천만 엔(USD 100,000 이상)이고 3D 프린팅이 그 비용을 크게 줄일 수 있다는 것입니다. 또한 3D 프린팅은 프로세스를 보다 효율적으로 만들어 설계 변경 사항에 더 빠르게 대응할 수 있는 유연성을 제공합니다.
SANKI의 CEO인 Ozo Mori는 다음과 같이 말했습니다. “FUNMAT PRO 410의 빌드 볼륨은 최대 305x305x406mm입니다. 이 시스템은 개방형 재료 시스템을 포함하며 복잡한 부품을 인쇄할 수 있는 수용성 지지 재료의 사용을 지원합니다. 내장된 선형 가이드와 고성능 방향 드라이브를 통해 FUNMAT PRO 410은 고속, 고정밀 3D 프린팅을 달성할 수 있으며, 이는 궁극적으로 맞춤형 프로세스를 크게 단축하고 비용을 효과적으로 절감하는 데 도움이 됩니다. 향후 FUNMAT PRO 410을 활용해 재난구조 및 긴급구조에 사용되는 특수차량용으로 특별히 설계된 공조 및 환기 파이프 부품을 소량 생산할 계획입니다.”
SANKI는 특히 FUNMAT PRO 410을 사용하여 나일론 유리 섬유(PA-GF) 환기 파이프 부품을 인쇄합니다. PA-GF는 일반 엔지니어링 플라스틱에 비해 인장강도, 굽힘강도, 열변형온도, 재료탄성률이 향상되었습니다. 이는 열 변형 및 재료 수축을 줄이는 데 도움이 됩니다.
자동차 배관 부품 테스트를 위한 3D 프린팅 고정구
3D 프린팅은 빠르고 정확한 생산 방법을 제공하여 도구 생산 비용과 시간을 크게 줄입니다. 그 결과 자동차 제조업체는 생산 능력, 효율성 및 품질을 빠르게 개선했습니다. 과거에는 알루미늄을 절단하여 복잡한 형상의 검사 지그를 제작하고 생산 시간이 길었습니다. 3D 프린팅이 구현되면 이 시간이 크게 단축되었습니다.
일본 Kanto에 위치한 자동차 부품 제조업체는 연간 매출이 1,000억 엔(미화 약 10억 달러)이며 INSTAMSYS FUNMAT PRO 410을 사용하여 Canon의 자동 배관 부품용 PC-ABS 테스트 고정구를 인쇄합니다.
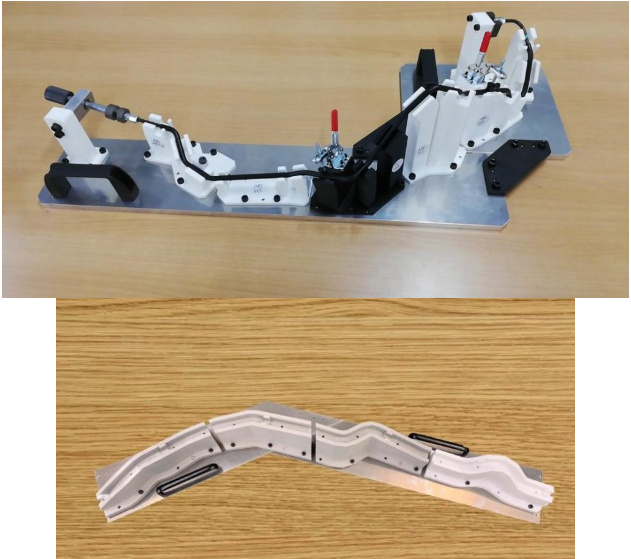
기술부장은 “3D프린터로 기존 절단 공정을 대체해 우리 공장 장비에서 소모성 부품을 생산한 후 일부 부품이 파손되더라도 즉시 3D 프린팅해 생산할 수 있어 생산이 가능하다”고 말했다. 지연 없이 신속하게 재개되어 배달 시간을 크게 단축합니다. 공장 설비의 소모성 부품은 160도 내열성이 요구되기 때문에 프린팅은 INTAMSYS의 PEEK 소재를 사용합니다. 인쇄 후 부품은 어닐링(비정질화) 없이 사용할 수 있으며 매우 견고합니다. 또한 회사는 회사 생산 장비의 개발 및 시험 생산을 위해 3D 프린팅을 사용합니다.”